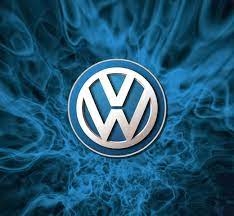
While Tesla begins production at its new German plant this month, Volkswagen is just weeks away from finalising plans for a 2 billion euro ($2.2 billion) electric vehicle (EV) factory that it hopes will catch up to its American competitor.
Tesla claims that its new Giga Berlin-Brandenburg facility in Gruenheide, near Berlin, can already produce a Model Y in 10 hours, but Volkswagen's ID.3 electric car takes three times as long.
With its "Trinity" EV factory, set to open in 2026, the German auto giant is now aiming to reduce production times by employing processes such as big die casting and reducing the number of components in its cars by a factor of several.
"Our goal is clear: we want to set the standard with our production," Volkswagen brand production chief Christian Vollmer told Reuters in an interview. "If we can get to 10 hours, we have achieved something big."
The carmaker has been increasing productivity at a rate of roughly 5% per year, but it needs to make bigger leaps to maintain its lead in the European market, according to Vollmer, who did not specify a new percentage objective.
Volkswagen, the world's second-largest carmaker after Toyota, has a 25 per cent share of the European EV market, ahead of Tesla's 13 per cent. Volkswagen boasts a stable of brands ranging from Skoda, Seat, and VW to Audi, Porsche, and Bentley.
However, Tesla's presence in Germany has increased the pressure on German carmakers to master and ramp up EV production, and Volkswagen Chief Executive Herbert Diess has cautioned that Germans must speed up to avoid being defeated on their own land.
Volkswagen's ambitions are in line with a broader industry trend of reducing product lines and streamlining manufacturing as automakers race to find the cash to support the electric transition - and keep up with rivals like Tesla, which don't have to juggle making EVs and gasoline-powered cars.
"Tesla really ignited the drive for reducing part counts and making simpler products," Evan Horetsky, a partner at McKinsey who was formerly in charge of engineering at Tesla's new Brandenburg plant, said. "Legacy manufacturers have a more difficult time because they have to maintain current orders."
One of the reasons Tesla can build its Model Y vehicles in Germany in under 10 hours, according to a Tesla spokeswoman, is that it utilises two massive casting presses, known as giga-presses, that exert 6,000 tonnes metal pressure to the back of the car.
In less than six minutes, its Gruenheide press shop can make 17 components. With six additional giga-presses on the way, Tesla will soon be able to make the front end of the car as well.
"That's why we're so fast," the spokesperson said.
Tesla popularised the giga-casting technique, which VW hopes to use, as a less labor-intensive alternative to manufacturing several stamped metal panels with crumple zones to absorb energy after an accident.
BMW, the German luxury carmaker, has previously rejected massive castings on the grounds that the greater repair costs offset the cheaper manufacturing costs.
However, proponents argue that automatic driving will limit the number of accidents: "Tesla is building a vehicle that will most likely not be in a major incident," said Cory Steuben, owner of manufacturing consulting firm Munro & Associates.
While VW can create some models like the Tiguan or Polo in 18 and 14 hours in Germany and Spain, the electric ID.3 takes 30 hours to put together in a factory that handles six vehicles from three Volkswagen brands.
Multiple work phases will be condensed into one at the Trinity facility through automation, decreasing the body shop and reducing the number of positions needing painful physical labour, according to Vollmer, who called it an expansion of "human-robot cooperation."
Volkswagen does not intend to install giga-presses at its new Wolfsburg plant, instead opting to use equipment from its factory in Kassel, approximately 160 kilometres (100 miles) away, and ship the items by train.
Tesla's Gruenheide facility is expected to produce 54,000 cars in 2022, 280,000 in 2023, and 500,000 by 2025, according to JPMorgan.
Volkswagen has not yet established an output target for Trinity, which will employ its Scalable Systems Platform and delivered 452,000 battery-electric vehicles globally last year.
It plans to produce 40 million vehicles on the new platform, which merges various internal combustion engine and electric platforms into one, by 2030, with half of its global output being all-electric.
Tesla, which produced 936,000 cars last year, has stated that by the end of the decade, it hopes to have produced 20 million vehicles, about quadruple the present annual production of Toyota, the world's largest automaker.
Nonetheless, as Tesla expands in Germany, it will face numerous challenges, ranging from securing more water supplies to environmental groups concerned about light pollution and traffic near the plant to unions concerned about a management-heavy works council and wages being driven down by foreign workers.
"Starting production is nice, but volume production is the hard part," Musk told a cheering audience at a festival at the plant site in October 2021. "It will take longer to reach volume production than it took to build the factory."
(Source:www.usnews.com)
Tesla claims that its new Giga Berlin-Brandenburg facility in Gruenheide, near Berlin, can already produce a Model Y in 10 hours, but Volkswagen's ID.3 electric car takes three times as long.
With its "Trinity" EV factory, set to open in 2026, the German auto giant is now aiming to reduce production times by employing processes such as big die casting and reducing the number of components in its cars by a factor of several.
"Our goal is clear: we want to set the standard with our production," Volkswagen brand production chief Christian Vollmer told Reuters in an interview. "If we can get to 10 hours, we have achieved something big."
The carmaker has been increasing productivity at a rate of roughly 5% per year, but it needs to make bigger leaps to maintain its lead in the European market, according to Vollmer, who did not specify a new percentage objective.
Volkswagen, the world's second-largest carmaker after Toyota, has a 25 per cent share of the European EV market, ahead of Tesla's 13 per cent. Volkswagen boasts a stable of brands ranging from Skoda, Seat, and VW to Audi, Porsche, and Bentley.
However, Tesla's presence in Germany has increased the pressure on German carmakers to master and ramp up EV production, and Volkswagen Chief Executive Herbert Diess has cautioned that Germans must speed up to avoid being defeated on their own land.
Volkswagen's ambitions are in line with a broader industry trend of reducing product lines and streamlining manufacturing as automakers race to find the cash to support the electric transition - and keep up with rivals like Tesla, which don't have to juggle making EVs and gasoline-powered cars.
"Tesla really ignited the drive for reducing part counts and making simpler products," Evan Horetsky, a partner at McKinsey who was formerly in charge of engineering at Tesla's new Brandenburg plant, said. "Legacy manufacturers have a more difficult time because they have to maintain current orders."
One of the reasons Tesla can build its Model Y vehicles in Germany in under 10 hours, according to a Tesla spokeswoman, is that it utilises two massive casting presses, known as giga-presses, that exert 6,000 tonnes metal pressure to the back of the car.
In less than six minutes, its Gruenheide press shop can make 17 components. With six additional giga-presses on the way, Tesla will soon be able to make the front end of the car as well.
"That's why we're so fast," the spokesperson said.
Tesla popularised the giga-casting technique, which VW hopes to use, as a less labor-intensive alternative to manufacturing several stamped metal panels with crumple zones to absorb energy after an accident.
BMW, the German luxury carmaker, has previously rejected massive castings on the grounds that the greater repair costs offset the cheaper manufacturing costs.
However, proponents argue that automatic driving will limit the number of accidents: "Tesla is building a vehicle that will most likely not be in a major incident," said Cory Steuben, owner of manufacturing consulting firm Munro & Associates.
While VW can create some models like the Tiguan or Polo in 18 and 14 hours in Germany and Spain, the electric ID.3 takes 30 hours to put together in a factory that handles six vehicles from three Volkswagen brands.
Multiple work phases will be condensed into one at the Trinity facility through automation, decreasing the body shop and reducing the number of positions needing painful physical labour, according to Vollmer, who called it an expansion of "human-robot cooperation."
Volkswagen does not intend to install giga-presses at its new Wolfsburg plant, instead opting to use equipment from its factory in Kassel, approximately 160 kilometres (100 miles) away, and ship the items by train.
Tesla's Gruenheide facility is expected to produce 54,000 cars in 2022, 280,000 in 2023, and 500,000 by 2025, according to JPMorgan.
Volkswagen has not yet established an output target for Trinity, which will employ its Scalable Systems Platform and delivered 452,000 battery-electric vehicles globally last year.
It plans to produce 40 million vehicles on the new platform, which merges various internal combustion engine and electric platforms into one, by 2030, with half of its global output being all-electric.
Tesla, which produced 936,000 cars last year, has stated that by the end of the decade, it hopes to have produced 20 million vehicles, about quadruple the present annual production of Toyota, the world's largest automaker.
Nonetheless, as Tesla expands in Germany, it will face numerous challenges, ranging from securing more water supplies to environmental groups concerned about light pollution and traffic near the plant to unions concerned about a management-heavy works council and wages being driven down by foreign workers.
"Starting production is nice, but volume production is the hard part," Musk told a cheering audience at a festival at the plant site in October 2021. "It will take longer to reach volume production than it took to build the factory."
(Source:www.usnews.com)