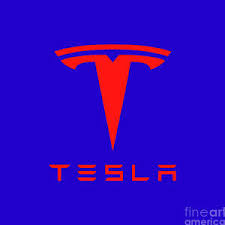
Tesla had merged a number of advances into a technological leap forward that might change the way it produces electric vehicles and aid Elon Musk in achieving his goal of halving production costs, according to report quoting sources with knowledge of the matter.
The business invented the "gigacasting" technology, which reduced production costs and forced competitors to catch up, by using massive presses with 6,000 to 9,000 tonnes of clamping pressure to mould the front and back structures of its Model Y.
According to the sources, Tesla is getting close to a breakthrough that would enable it to die cast almost all of the intricate underbody of an EV in a single piece, as opposed to the roughly 400 parts in a normal car, in an effort to increase its lead.
According to the reports, the know-how is essential to Tesla's "unboxed" manufacturing approach, which Chief Executive Musk outlined in March. It is a cornerstone of his aim to produce tens of millions of less expensive EVs over the next 10 years while still turning a profit.
Although Tesla has stated that their unboxed model entails simultaneously generating massive sub-assemblies of a car and snapping them together, the size and composition of the modular blocks are still up for debate.
According to Terry Woychowski, head of the American engineering firm Caresoft Global, if Tesla is successful in gigacasting the majority of an electric vehicle's undercarriage, it will further alter how cars are created.
"It is an enabler on steroids. It has a huge implication for the industry, but it's a very challenging task," said Woychowski, who worked for U.S. automaker GM (GM.N) for more than three decades. "Castings are very hard to do, especially the bigger and the more complicated."
The individuals in the stories claim that Tesla's previously unknown revolutionary design and production procedures allowed the business to construct a car from the ground up in 18 to 24 months, as opposed to the three to four years it typically takes most competitors.
The five individuals said that a single huge frame, integrating the front and back parts with the centre underbody where the battery is located, could be utilised in Tesla's tiny EV, which company plans to introduce by the middle of the decade with a starting price of $25,000.
Three of the sources claimed that Tesla would decide this month whether to die cast the platform in one piece, albeit even if they do, the final product may vary during the design validation process.
There were no comments from Tesla or Musk on the issues in the reports.
The innovation made by Tesla focuses on how massive moulds for such a large item are created and tested for mass manufacturing, as well as how casts might include hollow subframes with internal ribs to reduce weight and increase crashworthiness.
According to the five people, the breakthroughs in both cases include 3D printing and industrial sand and were created by design and casting experts in Britain, Germany, Japan, and the United States. The reports did not quote any of the sources because they were not authorised to speak on the issue to the media.
The "gigacast dilemma" is the reason why automakers have so far refrained from casting ever-larger structures: while building moulds to create pieces 1.5 metres squared or larger increases efficiency, doing so is expensive and fraught with numerous risks.
Changing the design of a huge metal test mould after it has been built may cost $100,000 per time, or remaking the mould entirely could cost $1.5 million, according to one casting specialist. Another stated that the total expense of designing a huge metal mould would be around $4 million.
That has been judged prohibitive by automakers, especially given that a design may require six or more changes to get a flawless die in terms of fit and finish, ergonomics, noise and vibration, and crashworthiness, according to the sources.
Despite the dangers, the sources claimed that Musk's original goal was to find a way to cast the underbody in one piece.
Tesla went to businesses that use 3D printers to create test moulds from industrial sand to get around the challenges. Binder jet printers use digital design files to print a liquid binding agent over a tiny layer of sand, layer by layer creating a mould that can die cast molten alloys.
Even with many iterations, the cost of the design validation process using sand casting is said to be low - only 3% of doing the same with a metal prototype.
That means Tesla can iterate on prototypes as often as necessary, printing a fresh one in a matter of hours with the help of equipment from businesses like Desktop Metal (DM.N) and its subsidiary ExOne.
According to two sources, the design validation cycle for sand casting only takes two to three months, as opposed to the six to twelve months it can take for metal mould prototypes.
Because they are hollow, the subframes in a car's underbody are typically lighter and more crash-resistant.
They are now created by stamping and joining many sections with a gap in the centre.
Tesla intends to insert solid sand cores created by the binder jets within the overall mould in order to cast subframes with hollows as part of one gigacasting. The sand is taken out to reveal the voids once the part has been cast.
Despite the intricacy of the big frames and the increased design flexibility, there was still a significant obstacle to overcome.
The castings' aluminium alloys performed differently in sand and metal moulds and frequently fell short of Tesla's requirements for crashworthiness and other characteristics.
Three of the sources claimed that the casting experts addressed this by creating specific alloys, optimising the molten alloy cooling procedure, and also developing an after-production heat treatment. Additionally, Tesla can spend money on a final metal mould for mass manufacturing once it is satisfied with the prototype.
The upcoming small cars Tesla is developing - one for personal use and the other a robotaxi - don't have a lot of a front "overhang" or a rear trunk, according to the sources, giving it the perfect opportunity to cast an EV platform in one piece.
"It's like a boat in a way, a battery tray with small wings attached to both ends. That would make sense to do in one piece," one person said.
However, the sources claimed that Tesla still needed to decide which type of gigapress to employ if it chose to cast the underbody in a single piece. This decision would also determine how intricate the car frame would be.
The people said Tesla would need new, larger gigapresses with tremendous clamping powers of 16,000 tonnes or more, which would be expensive and could require larger factory buildings in order to produce such vast body parts quickly.
However, according to three of the five sources, one issue with presses using strong clamping force is that they cannot accommodate the 3D-printed sand cores required to create hollow subframes.
They claimed that Tesla might overcome these challenges by utilising a different kind of press into which molten alloy may be progressively poured. This technique tends to produce castings of greater quality and can tolerate sand cores.
But the procedure goes more slowly.
"Tesla could still choose high-pressure for productivity, or they could choose slow alloy injection for quality and versatility," one of the people said. "It's still a coin toss at this point."
(Source:www.theprint.in)
The business invented the "gigacasting" technology, which reduced production costs and forced competitors to catch up, by using massive presses with 6,000 to 9,000 tonnes of clamping pressure to mould the front and back structures of its Model Y.
According to the sources, Tesla is getting close to a breakthrough that would enable it to die cast almost all of the intricate underbody of an EV in a single piece, as opposed to the roughly 400 parts in a normal car, in an effort to increase its lead.
According to the reports, the know-how is essential to Tesla's "unboxed" manufacturing approach, which Chief Executive Musk outlined in March. It is a cornerstone of his aim to produce tens of millions of less expensive EVs over the next 10 years while still turning a profit.
Although Tesla has stated that their unboxed model entails simultaneously generating massive sub-assemblies of a car and snapping them together, the size and composition of the modular blocks are still up for debate.
According to Terry Woychowski, head of the American engineering firm Caresoft Global, if Tesla is successful in gigacasting the majority of an electric vehicle's undercarriage, it will further alter how cars are created.
"It is an enabler on steroids. It has a huge implication for the industry, but it's a very challenging task," said Woychowski, who worked for U.S. automaker GM (GM.N) for more than three decades. "Castings are very hard to do, especially the bigger and the more complicated."
The individuals in the stories claim that Tesla's previously unknown revolutionary design and production procedures allowed the business to construct a car from the ground up in 18 to 24 months, as opposed to the three to four years it typically takes most competitors.
The five individuals said that a single huge frame, integrating the front and back parts with the centre underbody where the battery is located, could be utilised in Tesla's tiny EV, which company plans to introduce by the middle of the decade with a starting price of $25,000.
Three of the sources claimed that Tesla would decide this month whether to die cast the platform in one piece, albeit even if they do, the final product may vary during the design validation process.
There were no comments from Tesla or Musk on the issues in the reports.
The innovation made by Tesla focuses on how massive moulds for such a large item are created and tested for mass manufacturing, as well as how casts might include hollow subframes with internal ribs to reduce weight and increase crashworthiness.
According to the five people, the breakthroughs in both cases include 3D printing and industrial sand and were created by design and casting experts in Britain, Germany, Japan, and the United States. The reports did not quote any of the sources because they were not authorised to speak on the issue to the media.
The "gigacast dilemma" is the reason why automakers have so far refrained from casting ever-larger structures: while building moulds to create pieces 1.5 metres squared or larger increases efficiency, doing so is expensive and fraught with numerous risks.
Changing the design of a huge metal test mould after it has been built may cost $100,000 per time, or remaking the mould entirely could cost $1.5 million, according to one casting specialist. Another stated that the total expense of designing a huge metal mould would be around $4 million.
That has been judged prohibitive by automakers, especially given that a design may require six or more changes to get a flawless die in terms of fit and finish, ergonomics, noise and vibration, and crashworthiness, according to the sources.
Despite the dangers, the sources claimed that Musk's original goal was to find a way to cast the underbody in one piece.
Tesla went to businesses that use 3D printers to create test moulds from industrial sand to get around the challenges. Binder jet printers use digital design files to print a liquid binding agent over a tiny layer of sand, layer by layer creating a mould that can die cast molten alloys.
Even with many iterations, the cost of the design validation process using sand casting is said to be low - only 3% of doing the same with a metal prototype.
That means Tesla can iterate on prototypes as often as necessary, printing a fresh one in a matter of hours with the help of equipment from businesses like Desktop Metal (DM.N) and its subsidiary ExOne.
According to two sources, the design validation cycle for sand casting only takes two to three months, as opposed to the six to twelve months it can take for metal mould prototypes.
Because they are hollow, the subframes in a car's underbody are typically lighter and more crash-resistant.
They are now created by stamping and joining many sections with a gap in the centre.
Tesla intends to insert solid sand cores created by the binder jets within the overall mould in order to cast subframes with hollows as part of one gigacasting. The sand is taken out to reveal the voids once the part has been cast.
Despite the intricacy of the big frames and the increased design flexibility, there was still a significant obstacle to overcome.
The castings' aluminium alloys performed differently in sand and metal moulds and frequently fell short of Tesla's requirements for crashworthiness and other characteristics.
Three of the sources claimed that the casting experts addressed this by creating specific alloys, optimising the molten alloy cooling procedure, and also developing an after-production heat treatment. Additionally, Tesla can spend money on a final metal mould for mass manufacturing once it is satisfied with the prototype.
The upcoming small cars Tesla is developing - one for personal use and the other a robotaxi - don't have a lot of a front "overhang" or a rear trunk, according to the sources, giving it the perfect opportunity to cast an EV platform in one piece.
"It's like a boat in a way, a battery tray with small wings attached to both ends. That would make sense to do in one piece," one person said.
However, the sources claimed that Tesla still needed to decide which type of gigapress to employ if it chose to cast the underbody in a single piece. This decision would also determine how intricate the car frame would be.
The people said Tesla would need new, larger gigapresses with tremendous clamping powers of 16,000 tonnes or more, which would be expensive and could require larger factory buildings in order to produce such vast body parts quickly.
However, according to three of the five sources, one issue with presses using strong clamping force is that they cannot accommodate the 3D-printed sand cores required to create hollow subframes.
They claimed that Tesla might overcome these challenges by utilising a different kind of press into which molten alloy may be progressively poured. This technique tends to produce castings of greater quality and can tolerate sand cores.
But the procedure goes more slowly.
"Tesla could still choose high-pressure for productivity, or they could choose slow alloy injection for quality and versatility," one of the people said. "It's still a coin toss at this point."
(Source:www.theprint.in)